Statt "Downcycling": Tapes aus recycelten Carbonfasern für den Leichtbau
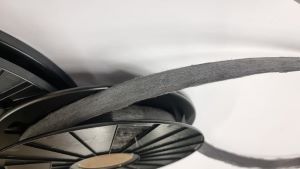
In Leichtbauanwendungen, bei denen eine hohe Festigkeit und Steifigkeit
bei zugleich minimalem Gewicht entscheidend sind, werden zunehmend
carbonfaserverstärkte Kunststoffe (CFK) eingesetzt.
Jedoch gehen mit dem
wachsenden Einsatz an CFK auch große Mengen an Carbonfaserabfällen einher.
Herkömmliche Recyclingverfahren verringern signifikant die CFK-
Eigenschaften und schränken die Einsatzbereiche ein. Die Deutschen
Institute für Textil- und Faserforschung Denkendorf (DITF) haben
hochorientierte Tapes aus recycelten Carbonfasern (rCF) entwickelt, die
auch für Hochleistungsanwendungen wie Strukturbauteile im Automobil
wiedereingesetzt werden können.
Carbonfasern werden in der Regel aus erdölbasierten Rohstoffen in einem
energieintensiven Prozess hergestellt, wobei große Mengen CO2 ausgestoßen
werden. Das verwendete Material entspricht einem Treibhauspotential von
ungefähr 20 – 65 Kilogramm CO2-Äquivalenten pro Kilogramm. Trotzdem steigt
die Produktion von CFK weiterhin und mit ihr auch die Menge an CFK-
Abfällen. Denn je nach Verarbeitungsverfahren fällt in der Produktion bis
zu 50 Prozent Verschnitt an. Hinzu kommen große Mengen CFK-Abfälle in Form
von Bauteilen, die das Ende ihrer Lebenszeit erreicht haben. Allein in
Europa werden bis 2030 voraussichtlich etwa 8.000 Passagierflugzeuge mit
erheblichen Anteilen an CFK aus dem Betrieb genommen.
Aktuell werden lediglich 15 Prozent der CFK-Abfälle rezykliert. Die
übrigen über 85 Prozent dieser CFK-Bauteile landen am Ende ihrer
Lebensdauer in Müllverbrennungsanlagen oder Deponien. Durch die
Verbrennung kann zwar Energie in Form von Wärme oder Strom gewonnen
werden. Ein Recycling der Carbonfasern würde jedoch weit mehr für den
Klima- und Ressourcenschutz beitragen.
In den letzten Jahren wurden deshalb verschiedene Recyclingverfahren für
CFK, wie die Pyrolyse oder Solvolyse, weiterentwickelt, um Carbonfasern in
hoher Qualität zurückzugewinnen.
Im Vergleich zu Neufasern sind die Einsatzmöglichkeiten von recycelten
Carbonfasern deutlich eingeschränkt. In einem Neufaserprodukt liegen
Carbonfasern üblicherweise in Filamentsträngen von technisch unbegrenzter
Länge und zudem in Lastrichtung orientiert vor. Auf diese Weise entfaltet
die Carbonfaser ihr volles Potential, da sie ihre maximale Festigkeit in
Faserrichtung aufweist. Durch das Recycling kommt es zwangsläufig zu einer
Einkürzung der Carbonfasern auf Längen im Mikrometer- bis
Zentimeterbereich. Zusätzlich geht die Lastrichtungsorientierung der
Carbonfasern verloren, die Fasern liegen zunächst in Wirrlage vor.
Die DITF befassen sich nun bereits seit ca. 15 Jahren erfolgreich damit,
die klassischen Spinnereiprozesse an das neuartige Fasermaterial rCF
anzupassen. Ziel ist es dabei, eine neue Kategorie von rCF-Tape-Halbzeugen
zu entwickeln und in ihren mechanischen Eigenschaften so zu verbessern,
dass sie Neufasermaterial in strukturellen Anwendungen tatsächlich
ersetzen kann. Nur dann sind carbonfaserbasierte Verbundwerkstoffe
wirklich kreislauffähig.
Um ein orientiertes Halbzeug ähnlich eines Carbonprodukts aus Neufasern
herzustellen, ist es entscheidend, die Wirrlage der rCF aufzuheben und die
Fasern wieder parallel zueinander auszurichten. Eine vielversprechende
Möglichkeit dies zu erreichen, stellt die Herstellung von hochorientierten
Tapes dar.
Hierbei werden die Carbonfasern in einem ersten Schritt geöffnet und mit
thermoplastischen Matrixfasern (Polyamid 6) gemischt. Im Anschluss wird
die Fasermischung in einem für die Verarbeitung von Carbonfasern
modifizierten Krempelprozess weiter separiert und orientiert. Am Auslauf
der Krempel wird das im Krempelprozess entstehende Faserflor zu einem
Faserband zusammengefasst und in eine Kanne abgelegt. Dieses
rCF/PA6-Faserband stellt das Ausgangsmaterial für den folgenden
Tapebildungs-Prozess dar und weist bereits eine Vororientierung der
Carbonfasern auf. Im nachfolgenden Verstreckprozess kann die Orientierung
der Fasern noch gesteigert werden. Durch das Verziehen des Faserbandes
werden die Fasern in Verzugsrichtung bewegt und längs ausgerichtet. Der
letzte Prozessschritt ist die Tapebildung, bei der das Faserband unter
Spannung in die gewünschte Form gebracht und anschließend in eine endlose
Tapestruktur fixiert wird. Bei der Fixierung schmelzen die
Thermoplastfasern teilweise oder komplett auf und erstarren anschließend.
Diese an den DITF entwickelte Technologie zur Herstellung von
hochorientierten rCF-Tapes wurde im Rahmen des Forschungsprojektes
„Infinity“ (03LB3006) eingesetzt, um einen nachhaltigen und
faserschonenden Recyclingkreislauf für CFK nachzuweisen. Auf Basis der
„Infinity“-Tapes wurde ein Verbundwerkstoff entwickelt, der 88 Prozent der
Zugfestigkeit und des Zugmoduls eines vergleichbaren Neufaserprodukts
erzielte. Zudem ergab eine Lebenszyklusanalyse, dass sich das
Treibhauspotenzial bei Einsatz von Pyrolysefasern um ca. 49 Prozent und
für rCF aus Produktionsabfällen um ca. 66 Prozent reduziert.
Die Ergebnisse weisen somit den Weg zur echten Substitution von Neufaser-
CFK durch Recycling-CFK anstelle des Downcyclings zu schwach orientierten
Materialien und dem damit verbundenen Verlust an mechanischen
Eigenschaften.